According to BLOX CEO Chris Giattina, off-site manufacturing presents a significant opportunity to revolutionize the way we “build” buildings in healthcare.
After working for decades as an architect, Giattina founded BLOX with one goal in mind: to simplify construction by building standardized, prefabricated modules that can be produced in a factory, then quickly assembled on-site. At the Health Facilities Innovation Forum (now HealthSpaces), Giattina shared the benefits of embracing prefab construction, proving that even facilities as complicated as hospitals can be built better, faster, and more affordable with a prefab approach.
When Your Process is Behind the Times, Your Results Will Be Too
For the past 50 years, the construction industry has been stuck in a downward slump. Productivity and growth have dropped, in turn causing costs to rise. The result is an outdated methodology (design-bid-build) that’s sucking budgets dry and producing lackluster results.
Giattina cites 3 top reasons why this stagnation came to be:
1. The construction industry is institutionally siloed. We’ve separated our responsibilities and purviews into tiny domains, crippling our ability to understand each other, work well together, and get a big-picture perspective.
2. We minimize our investments into research and development. Though we’re eager for construction to be cheaper, we don’t invest in making it happen--many of us forget that investments are made to get positive returns.
3. We’re not leveraging scale. Many construction professionals view every project as having different conditions. The only way to respond to this mindset is to use all the project’s unique parameters to come up with a unique solution. Yet despite starting from scratch every time, the solutions to these projects end up being strikingly similar.
If we want to start building healthcare facilities more efficiently, then we need to remedy the factors that make our current construction process so redundant, costly, and slow.
“We have to replace the current state with a framework that embraces manufacturing productivity in a fundamentally different way.”
-Chris Giattina, BLOX CEO
In his work through BLOX, Giattina has developed a new building delivery system, one that’s optimized for efficiency and ready for the future.
A 21st-Century Model: Design-Manufacture-Construct
Design-Manufacture-Construct (DMC) is built on three main tenets:
Reduced Complexity
DMC works to eliminate unnecessary complexities from the building area. While this shift does grow complexity in other areas, it majorly streamlines the building process. “We’re trying to remove complexity from the job site, but in order to do that, we actually have to increase complexity at a technology side, at an engineering side, at a transportation logistics side…” says Giattina.
Reproducible Quality
This model enables the production of reproducible components, something especially important given the shortage of skilled labor. In many cases, this requires implementing digitally controlled operations, but there’s also the matter of taking old school trades and rethinking how they’re processed.
Maximized Speed
With DMC, facility components like exam rooms and bathrooms are quickly built in a factory and delivered to the job site, ready to be integrated into the greater construction. This change from the stick-built approach allows for greater speed. Healthcare leaders can get their investments back sooner by having their facilities service-ready as fast as possible.
Giattina introduces two separate versions of the DMC model.
Version 1 is what he suggests should be implemented now. Instead of diving into complete prefabrication, this version only aims to remove 25% of the complexity from the job site, targeting the most complicated parts. These components will be handled in a Lean factory, which churns out modules that can easily be reproduced and inserted into many projects.
Version 2 is what Giattina says should be our ultimate goal; it’s how all facility construction should be done in the future. This version removes all complexity from the job site, offloading everything to factory production through standardized processes. With this approach, every part of the building can be prefabricated and then brought to the job site for integration. On-site construction is simply a matter of snapping the modules together.
If you’d like to learn more about prefab's potential to transform healthcare construction, watch the full presentation here:
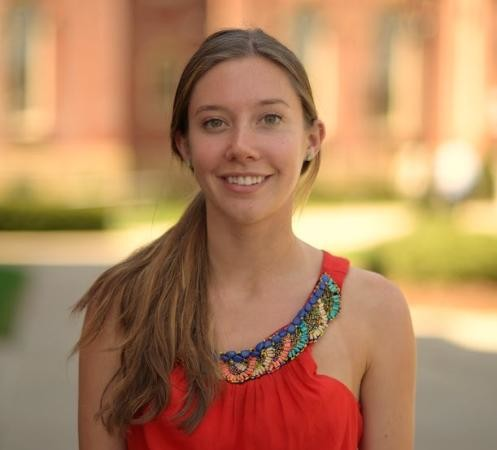
Posted by
Collaborate with your Peers!
HealthSpaces is a community for people that plan, design, build and operate spaces where healthcare is delivered.
June 7-9, 2026 | Destination TBA
Learn More
Comments